5 ways to optimize operations
- share
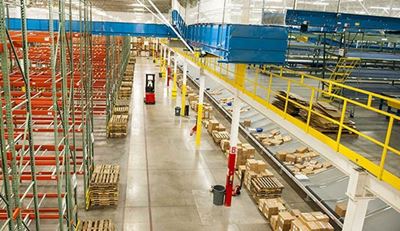
Dunn & Bradstreet reports that more than half of all Fortune 500 companies experience at least 1.6 hours of downtime each week, costing each company approximately $46 million in lost productivity annually. The costly implications of downtime underscore the importance of ensuring that operations run as efficiently as possible.
Dunn & Bradstreet reports that more than half of all Fortune 500 companies experience at least 1.6 hours of downtime each week, costing each company approximately $46 million in lost productivity annually. The costly implications of downtime underscore the importance of ensuring that operations run as efficiently as possible.
Lift trucks are a critical component of efficient operations. Think about it: Your organization won’t get paid unless customers are receiving their orders, and having an efficient lift-truck fleet is imperative to get product out the door.
With that in mind, here are five critical areas to assess to keep your lift-truck operations running as smoothly as possible:
- Right-size the truck for the job. Does battery life align with shift schedules? Are you losing productivity and uptime by changing batteries? Are you using the truck as you intended when it was purchased or do you now require the lift truck to be used for different purposes? Ensuring that you have the right truck for the job is an important way to enhance efficiency. The next time you need to add to your fleet or replace a truck, thoroughly examine how the truck will actually be used instead of simply ordering the same model as in the past. The same is true for your truck power.
- Optimize use. Track truck and operator data to help flag potential issues early or take advantage of opportunities to improve performance. It’s our experience that many operations teams feel they are using their lift trucks a lot more than they really are. Based on the data we’ve seen, fleets often are fully utilized for just 45% of a shift. Consider how you can rearrange operator schedules or processes to more fully utilize your fleet.
- Properly maintain your fleet. Don’t think of regular maintenance as an option—it really must be done consistently to achieve 100% uptime with your fleet. Additionally, address any issue—even seemingly small ones—as early as possible. For example, if a driver flat-spotted a tire and doesn’t take the truck into the shop ASAP, the result could be a catastrophic failure versus a simple repair.
- Have a fully trained professional service your fleet. From time to time, we hear of companies enlisting people with general facility maintenance responsibilities to maintain the company’s fleet of lift trucks. Fleet-truck maintenance requires a specialized skill set—one often not covered in training for general positions. Keeping up on maintenance with a trained professional is an important way to keep the fleet fully functional as much as possible.
- Don’t leave well enough alone. A commitment not only to collecting and analyzing data but also to acting on it is critical to improving productivity. Continually advocating for data-driven enhancements and changes (even if costs may be involved) can help spark conversations that lead to real, valuable, and significant improvements.
The bottom line is you can take steps to improve the performance of your lift-truck fleet to help mitigate the price tag associated with downtime.
Submitted on Fri, 05/27/2016 - 12:19
Plant Services, Today's Optimized Facility