New technology: Is it right for my operation?
- share
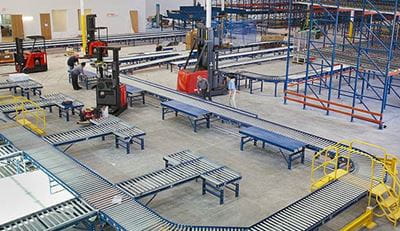
New and improved technologies developed specifically for batch picking or multiorder picking help increase warehouse productivity, eliminate errors, and save money when it comes to total cost of ownership. The question, however, is which technologies will provide the biggest return on investment? And when is the right time to buy this equipment?
The market is changing in response to consumer demand for more product variation, new products, and quicker delivery expectations. In turn, warehouse operations are demanding solutions that address space restraints, drive increased piece picking and case picking, and reduce pick errors—especially with increased e-commerce demand for direct delivery to end users.
New and improved technologies developed specifically for batch picking or multiorder picking help increase warehouse productivity, eliminate errors, and save money when it comes to total cost of ownership. The question, however, is which technologies will provide the biggest return on investment? And when is the right time to buy this equipment?
Innovations in batch picking applications
While batch picking for multiple customers at the same time can boost productivity, it can also increase pick errors. When selectors place a product on the wrong customer pallet and ship to the wrong end user, one customer receives a product he or she did not order and another customer won’t receive his or her product on time. Batch-picking operations report seeing an up to 25% increase in this type of pick error.
Fortunately for those in batch picking operations, innovations can help reduce picking errors. Although it can be difficult to justify the purchase of new warehousing technologies when upfront costs are high, these technologies can save customers money and time in the long run. Many customers have adopted voice pick technology to help increase productivity and pick accuracy. Voice picking delivers pick instructions to selectors, telling them which location to go to, which product to pick, how many of the item to select and for which customer the product is intended. However, the selector still directs placement on the pallet.
Managers can estimate the annual cost of mispicks by multiplying the mispick rate by the average mispick cost. A 2012 Newcastle study estimates the cost of mispicks on average to be $22 per case; however, the total cost could be as high as $100 per case when extra labor and delivery costs required to correct a mispick are factored in. The total number can be staggering —especially in high throughput applications.
Put-to-light technology uses LED lights to direct placement of product when order picking. Put-to-light systems can help grocery customers solve a unique business challenge and meet changing demands in an evolving market. Forward-thinking equipment and technology providers understand pain points and continuously provide innovations that deliver results. Similarly, forward-thinking operations that take advantage of such innovations will benefit in the long run.
Submitted by Sue Rice on Mon, 06/05/2017 - 17:47
Plant Services, Today's Optimized Facility
Read the original post: https://www.plantservices.com/blogs/todays-optimized-facility/new-technology-is-it-right-for-my-operation/