Understanding and improving your order picking
- share
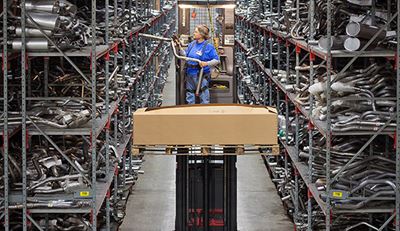
Industry challenges are creating tremendous pressure within warehouses and distribution centers, and having an efficient order-picking method can ease tensions.
Industry challenges are creating tremendous pressure within warehouses and distribution centers, and having an efficient order-picking method can ease tensions. Reducing the time from 15 seconds to 10 seconds per pick makes a big difference.
There are different order picking methods to choose from: traditional, semi-automated and fully automated. But first, let’s start with understanding what order picking means.
What is order picking?
Order picking is the process of locating and pulling product from your warehouse inventory to fulfill a customer order. From there, product is packed and shipped. While this process may sound simple, it is often more complicated than people would assume. How do you ensure you’re picking a product in the most efficient and productive way? How do you keep up with the ever-evolving challenges in the supply chain?
Traditional
Operators pick, replenish and let down items within their specified work zone for their approved operating equipment. Manual machines allow access to low-level and high-velocity product placement. As a general rule, employees should not pick, pack, or handle items larger than themselves (40 to 80 pounds is ideal). They should always follow established best practices
Retail and businesses selling fast-moving consumer goods with high SKU counts tend to benefit from traditional order-picking methods due to their verifiable accuracy without the need for expensive equipment and massive investments.
Semi-automated
Semi-automated pick options work alongside traditional order picking methods to increase picking efficiencies. Examples of semi-automated pick options include voice picking, RF scanning and pick-to-light technologies. These methods integrate automated and traditional picking solutions to make one’s warehouse more efficient.
Automated
Automated order picking follows the process of placing, picking, and retrieving items from their specified storage areas by using systems that integrate software with equipment and work in conjunction with a warehouse management system (WMS) or warehouse control system (WCS). Automated picking can result in greater productivity and efficiency because it reduces or eliminates the need for manual labor. It can also be more precise as the WMS integration reduces the chance of human error.
Due to their efficiency and adaptability, automated order picking methods are ideal for a wide range of industrial businesses.
Regardless of whether you opt for a traditional, semi-automated, or fully automated approach to order picking, each method can offer benefits for your warehouse. There are a few general best practices you can follow:
- Establish goals and tracking systems for stockouts and misplaced items to help avoid wasting time and effort by picking.
- Group items with similar SKUs in the same area to help reduce picking time and ensure that the space can handle high-volume activity.
- Optimize: Identifying and addressing your facility's specific needs as they pertain to container selection, picking methods, etc., will keep the warehouse running efficiently and productively.
As your business evolves and grows, your order picking process should, too. Check in regularly with warehouse managers and workers to see how your current system is working and whether there’s room for improvement.
Submitted by: Shannon Curtis, order pickers product manager, and Erica Moyer, pallet truck and stacker product manager, The Raymond Corp., and Shawn Turner, corporate warehouse product manager, Carolina Handling LLC.
Plant Services, Today's Optimized Facility
Read the original post: https://www.plantservices.com/blogs/todays-optimized-facility/understanding-and-improving-your-order-picking/